Исходным сырьем для изготовления автоклавного пенобетона является известь, кварцевый песок и цемент. Значительное
влияние на свойства пенобетона в автоклавной технологии оказывает тонкое измельчение сырьевых компонентов, обеспечивающее большую суммарную поверхность зерен, приводящее к большей однородности продукта. Поэтому при автоклавном производстве рекомендуется проводить помол песка и извести. Помол песка осуществляется в шаровых мельницах мокрым способом с водой, до определенной дисперсности. Значения удельной поверхности молотого песка, в зависимости от средней плотности ячеистого бетона составляют:
— для средней плотности D400 — 280-300 м2/кг;
— для средней плотности D500 — 270-290 м2/кг;
— для средней плотности D600 — 260-280 м2/кг;
  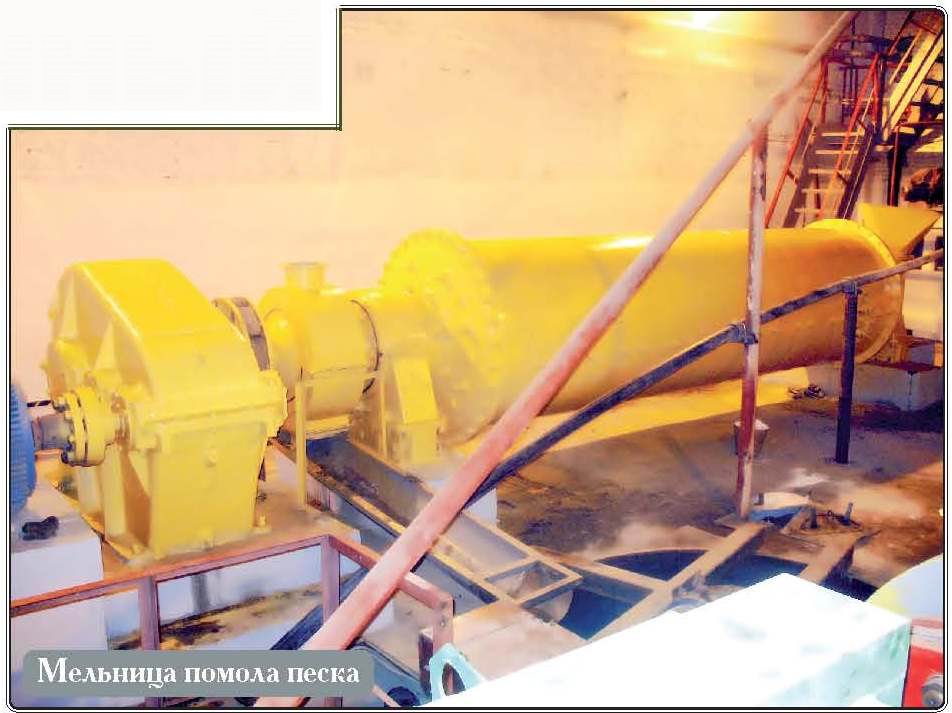
Полученный песчаный шлам складируется и усредняется в шламбассейне со встроенной мешалкой. Плотность используемого в технологии усредненного песчаного шлама равна 1,6 кг/м . Помол извести осуществляют в мельницах сухого помола вместе с песком для получения двухкомпонентного автоклавного вяжущего. Гидратация извести является процессом экзотермическим, то есть проходящим с выделением тепла — 270 ккал тепла на 1 кг негашеной извести. Поскольку эта реакция вызывает большой подъем температуры, особого внимания заслуживает вопрос устойчивости пены при повышении температуры и ограничения, связанные с возможным разрушением пенобетонной смеси. В связи с этим, температура смеси не должна превышать 30-35 С. Для обеспечения требуемых температурных ограничений высокоактивную известь подвергают перед помолом предварительному частичному гашению водой. Кроме того, частичное гашение извести можно регулировать количеством песка, подаваемого для совместного помола с известью при приготовлении известково-песчаного вяжущего.
Удельная поверхность вяжущего должна составлять 560-600 м /кг.
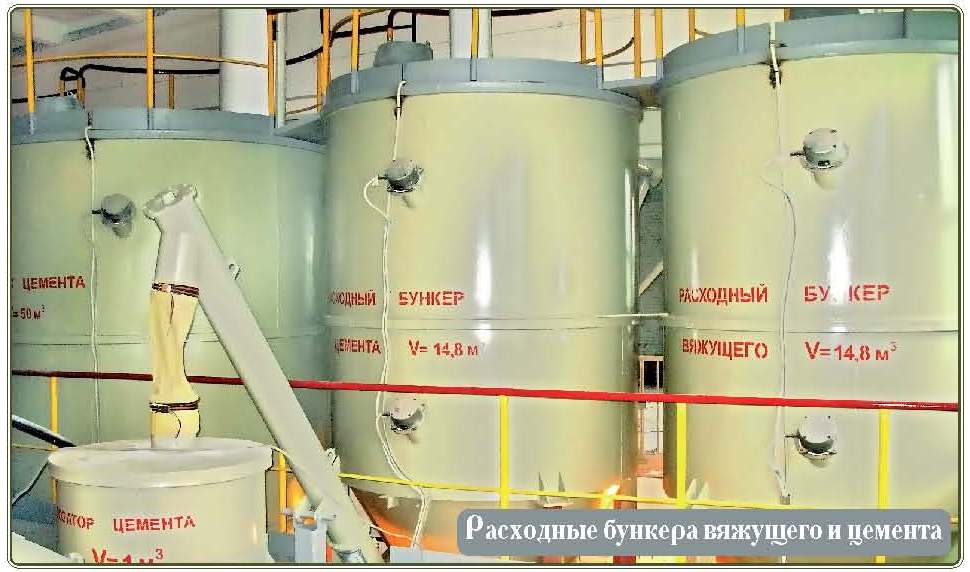  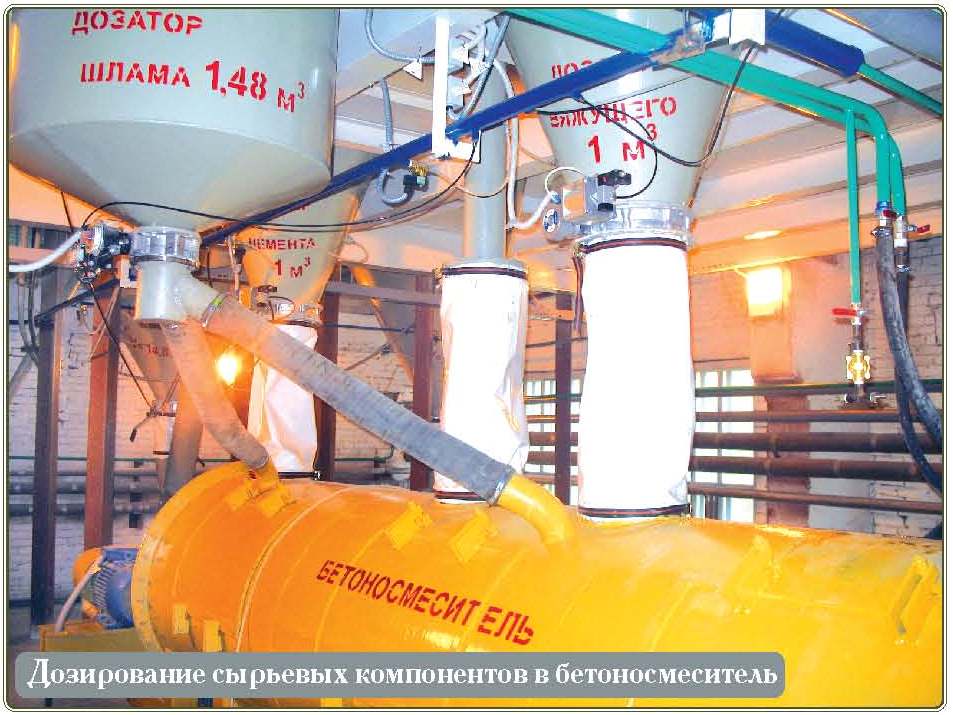
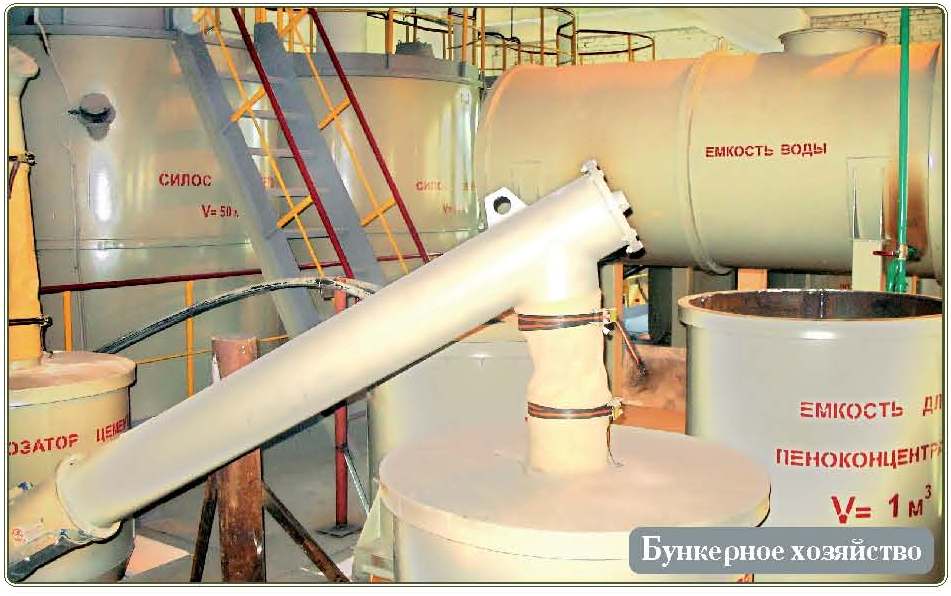  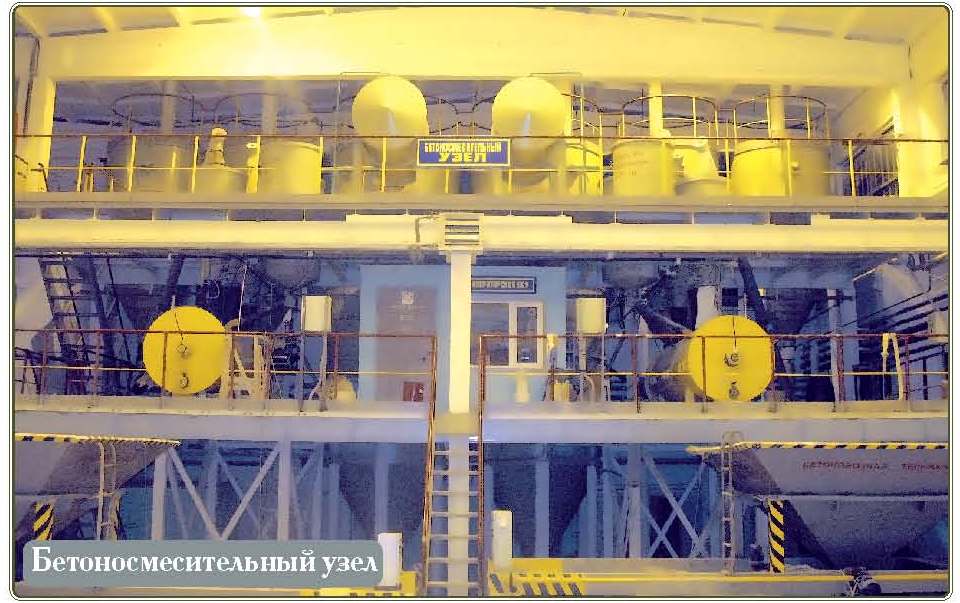
В смесеприготовительном отделении для приема материалов предусмотрено бункерное хозяйство, расходные бункера вяжущего и цемента и расходные емкости для песчаного и вторичного шлама. Все составляющие смеси взвешиваются на дозаторах с точностью ±2%.
 
Пенобетонная масса транспортируется с помощью бетоновозной тележки к постам формования, где происходит заливка приготовленной массы и ее выдержка в формах, расположенных неподвижно в камере при постоянной температуре и влажности.
При достижении массивом достаточной структурной прочности производится распалубка форм, и массив подается с помощью крана и траверса на резательный комплекс.
  
Приготовление раствора происходит в винтовом смесителе принудительного действия путем перемешивания основных компонентов с добавлением механически устойчивой пены, которую производят на специальном оборудовании – пеногенераторе. Количество смесителей, используемых в технологии – разное и определяется производительностью технологической линии.
На отдельных станциях резательного комплекса массивы сначала калибруются, а затем подвергаются вертикальной и горизонтальной резке на изделия заданных размеров. Резка массива производится короткими струнами, обеспечивающими высокую точность размеров и хорошую геометрию получаемых изделий. Конструктивные особенности резательного комплекса позволяют производить разрезку массивов с точностью резки ±1,0…1,5 мм.
  
Окончательный набор прочности происходит при отвержении пенобетон-ных блоков под давлением пара в автоклавах при давлении 0,8-1,2 МПа и температуре 174-182 С.
После автоклавной обработки полученные блоки отделяются друг от друга на делительном агрегате, с последующим пакетированием и упаковкой на поддонах.
  
|